一、前言 ElQ?|HsQ6p
快速成型技术是20世纪80年代后期发展起来的一项高新技术[1]。它不仅在制造原理上与传统方法全然不同,更重要的是在目前制造策略以市场响应速度为第一的方针状况下,可以缩短市场开发周期,降低开发成本,提高企业的竞争力。 -n05Z@7
快速成型技术具有以下优点:(1)技术集成度高,整个生产过程数字化;(2)制造成本与产品的复杂程度无关;(3)产品的单价几乎与批量无关;(4)绿色的加工技术。以累加思想实现零件制作的快速成型技术是制造技术领域的一项重大突破,其理论、工艺的完善以及精度的提高等,对快速成型技术的普及和应用有着极其重要的影响。 tsc`u>
成型加工过程中,必须保证一定的制作精度和表面质量,影响制件精度的因素是多方面的[2]。对成型加工精度的影响因素及改进措施的研究,对快速成型技术的发展和普及应用具有重要的意义[3,4]。本文试验所采用的快速成型设备是AFS快速成型机。 }aRib{L
二、数据处理误差 VQla.Y
2.1格式转换误差 [oTe8^@[
CAD模型的STL格式转换即是用三角形面片逼近实际模型表面,转换为所谓的事实上的标准文件格式。STL文件的精度等级不同,所产生的转换误差也不同。STL文件的精度是指用STL格式拟合最大允许误差。实际上,如果原几何模型完全由直边组成,则STL格式拟合绝对准确,没有任何误差;否则,存在拟合误差。例如同一个圆分别使用4个及6个三角形的STL格式表示,如图1所示。 g&FTX>wX
12n:)yQy
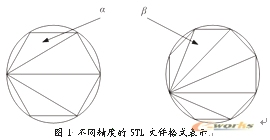
由此可见,精度要求越高,三角形面片的数目越多,它所表示的模型与实际模型就越逼近,但与此同时,STL文件数据量也将剧增,加大了后续数据处理的运算量。另外,三角形面片也会随精度提高而变小,在模型的细节部位会出现大量极为细小的三角形面片,增大数据处理的难度。而且在数据处理过程中常常产生致命的错误。因此,较好的方法是根据工艺条件和制件的精度要求选择适当的STL格式精度。 qazA,|L!
2.1 分层切片误差 /J#(8p
将CAD模型进行STL转换后,接着便要对其进行分层处理。分层是用一簇平行平面沿某一设定方向与STL模型求截交线得到轮廓信息。以半径为 的球体为例,如图2a所示,从中截出特定的一段,设其STL格式为图2b所示,这时其顶面和底面是距球心高度分别为 、 的两个圆,设其半径分别 、 。 @[3c1B6K
EhHxB
fAQ
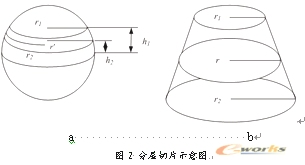

三、设备误差 U0_^6zd_
3.1 托板 方向运动误差 Zl5'%b$&
托板 方向运动误差直接影响堆积过程中层厚精度,最终导致Z方向产生尺寸误差,而托板在垂直面内的运动直线度误差,宏观上产生制件的形状、位置误差,微观上导致粗糙度值增大。因此,托板 方向系统要选用精密导轨、滚珠丝杠、伺服控制系统来提高 方向的运动精度。 O6;"cUv
3.2 X-Y方向同步带变形误差 G7CeWfS
X-Y扫描系统采用X-Y二维运动工作台,由步进电机驱动齿形同步带并带动光头运动。在定位时,由于同步带的变形,会影响定位的精度,常用的方法是通过设定位置补偿系数来减小其影响。为了考察其影响结果,我们在AFS快速成型机上加工制件,分别在采用补偿系数和未采用补偿系数两种情况下作了实验。 )SmnLvL
下表即为采用补偿系数和未采用补偿系数时所测得的制件的实际尺寸值,制件的名义尺寸分别为2,5,10,15,20,25mm,所使用的光斑补偿直径分别为1.0mm和1.1mm。
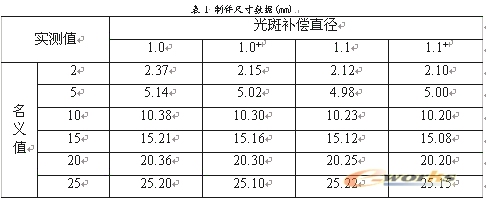
(注:表中带有+号表明设定了同步带变形补偿值,其中同步带的X方向的补偿系数为1.017,Y方向的补偿系数为1.022。) 6^Wep- $
将上表中的制件误差用图形表示更加直观,如图3所示,将制件的名义尺寸用水平轴表示,制件的尺寸偏差用垂直轴表示,根据以上实验数据做图如下:
从图3可以看出,在相同光斑补偿直径的情况下,考虑同步带变形补偿系数所得到的制件尺寸精度要高些。在这几种情况下使用1.1mm的光斑补偿直径并设定相应的补偿系数,制件的精度最高。 [7v|bd
3.3 X-Y方向扫描运动误差 1/Ts .\K3
扫描过程中,X-Y工作台存在以下问题: YqX$a~
(1)运动惯性力的影响 工作台在开始扫描阶段以恒定的加速度 从静止状态提高到设定扫描速度 ;在制动阶段,工作台以- 的加速度降低为静止状态,如图4所示。在一般情况下,工作台能很快地进入扫描状态,以速度 扫描,在临近另一个边缘处,速度逐渐降低为0。工作台在启动和制动阶段,存在一定的惯性,使得工作台在制件边缘部分将超出设计尺寸的范围,导致制件的尺寸有所增加。 C[^V\?3ly:
NGc~%0n
(2)工作台振动的影响 成型过程中,扫描机构对制件的截面作往复填充扫描,如图5所示。由于工作台在运动过程中本身具有一个固有频率,当扫描频率接近系统的固有频率时,振动增大,甚至出现共振现象,制件将产生较大的误差。 '}_r/l]K
-x//@8"
四、固化成型误差 p)IL(_X)
4.1 过固化误差 0\%g@j-aD
塑料粉末的固化宽度与深度是与其所吸收的激光平均能量有关的。扫描速度越低,平均能量越大,这时粉末固化宽度、深度越大,固化程度越高。在靠近制件边缘处,扫描速度越低,而且由于存在扫描方向的变换,形成一定时间的滞留,因此边缘处粉末固化程度较高,出现过固化。在这种情况下,当扫描一条直线时,直线的两端固化程度逐渐增加,固化线呈两头大、中间小的哑铃型,如图6所示。
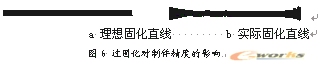
4.2 收缩变形误差 S!b18|o"
由于材料从粉末状到固态的聚合反应过程中要产生线性收缩和体积收缩,而线性收缩将导致在层堆积时产生层间应力,这种层间应力使制件变形,导致精度丧失。这种变形的机理复杂,与材料的成分、光敏性、聚合反应的速度有关。实践证明:通过开发低收缩、高强度的塑料粉末是提高制件精度的根本途径。而对同一性能的塑料粉末,通过合理选择制作工艺参数来提高制件精度也是一条有效的途径。
4.2 光斑补偿直径误差 X.t4;
相对于激光快速成型系统,AFS成型系统所用的光源形成的光斑直径要大一些,成型用的光点实际上是一个具有一定直径的光斑(塑料粉末面上光斑约0.5mm),成型中不能将光斑进似为光束能量聚集的光点,光能量分布在整个光斑范围内,实际制件轮廓是光斑中心运行轨迹上一系列固化点包络形成的,如图7所示。图中虚线部分为设计尺寸,在成型过程中光斑中心沿虚线运动,实线部分为实际成型制件,它是由固化点的包络线形成的。这一固化特点不仅增加了制件的尺寸,在其拐角处形成圆角,导致形状钝化,制件的轮廓形状变差,降低了制件形状精度,这使得一些小尺寸的制件用这种大直径的光斑无法加工。 $"kPzo~B_
@V*dF|# /
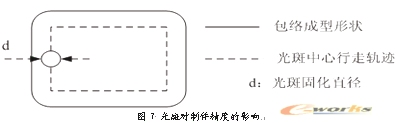
所以如果不采用补偿,所做出的制件实体部分实际上每侧大了一个光斑半径,使制件出现正偏差。为了减小或消除正偏差,采用光斑补偿,使光斑扫描路径向实体内部缩进一个光斑半径。从理论上说,光斑扫描按照向实体内部缩进一个光斑半径的路径扫描,所得制件的尺寸误差为零。 @z@%vr=vX
但是实际上,光斑直径是不容易控制的,它随着安装的状态不同而改变。由于AFS快速成型机无光斑测量机构,所以实际上的光斑直径大小是不可以直接测量的,需要根据制件误差大小修正补偿直径大小,使补偿直径大小等于实际光斑直径。
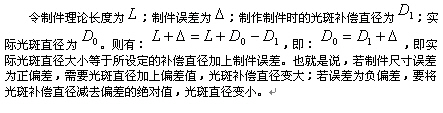
五、后处理误差 x z_sejKB
后处理是指整个制件加工完成后的辅助处理工艺,包括制件的清洗、打磨、表面喷涂以及后固化处理。在后固化时,残留粉末固化不均匀收缩引起制件变形,产生后处理误差。因此,研究具有良好性能的粉末材料可减小因此对精度的影响。 ! K>iSF<
六、几种可能的改进措施 A;TP~xq\
通过对影响制件精度的各种因素的分析,可对现有的设备提出以下几种可能的改进措施: A0DGDr PD
(1)对工作台进行运动平衡 固化成型过程中,工作台的运动精度是制约制件质量的一个关键因素。不仅工作台的静态工作特性(X、Y方向导轨的直线度、配合部件之间的摩擦系数以及工作台的定位精度等)影响制件精度,由于成型扫描是往复运动的过程,尽量减轻工作台的质量以减少惯性,通过调整工作台的阻力系数以减少惯性的影响。另一方面,适当提高工作台运动加速度,可以减小速度转化时间,缩小制件过固化的区域。 LCHMh6
(2)增加挡光系统 针对扫描系统加减速特征,在光路系统的前端增加挡光片,当工作台处于加速或减速阶段时,挡光片阻挡光线传输到光纤,只有达到正常扫描速度时,挡光片让开,使系统正常扫描固化,避免了制件边缘过固化现象,提高制件的尺寸精度,同时改善轮廓质量。 j<<d A[X
(3)适量增加光斑补偿 成型过程中的制件外形尺寸,实际是一系列光斑的包络线包络形成的,光斑补偿的方法是通过修改制件的CAD数据尺寸,在成型过程中原制件的边界等距离收缩一定数值,与光斑直径的增加量互相补偿,光斑补偿直径的大小主要取决与粉末平面处的光斑大小,同时考虑其他的因素的影响。在实际过程中,补偿直径的数值的大小是通过实验确定。
;/K2h_=3z
(4)适当调整定位补偿参数 将同步齿形带变形的影响考虑在内,根据下面的公式进行修正:定位补偿参数=名义尺寸值/实测值 默认的补偿系数 cszvt2BIg
通过应用上述改进措施,制件的精度有所提高,如图10所示。
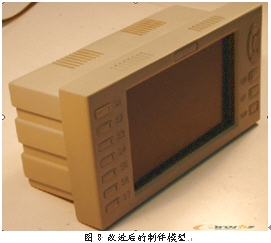
七、结论 P3_.U8g$r
本文通过对影响制件精度的各种因素的分析,以及将对工作台进行运动平衡、增加挡光系统、适量增加光斑补偿、适当调整定位补偿参数等改进措施应用于试验,得到了精度较高的制件。由此说明,本文所分析的各种影响因素及所采取的改进措施是正确的。 <sH}X$/
(&:gD4.
[参考文献] ~Bzzu %S
[1] 王秀峰, 罗宏杰. 快速原型制造技术. 中国轻工业出版社. 2001. IP62|~Ap
[2] 王从军, 李湘生, 黄树槐. SLS成型的精度分析. 华中科技大学学报. 2001. ShB]U5b:k
[3] Hope R L, Roth R N, Facobs P A. Adaptive Slicing with Sloping Layer Surfaces. Rapid Prototyping Journal.1997. EA& 3rI>U)
[4] 樊自田, 黄乃瑜, 肖跃加, 韩伟. 基于选择性烧结制件的精度分析. 南昌大学学报. 2000.